
Development of a vortex in a pumping chamber: physical model tests constitute a test case for calibration of a numerical model.
7 January 2020
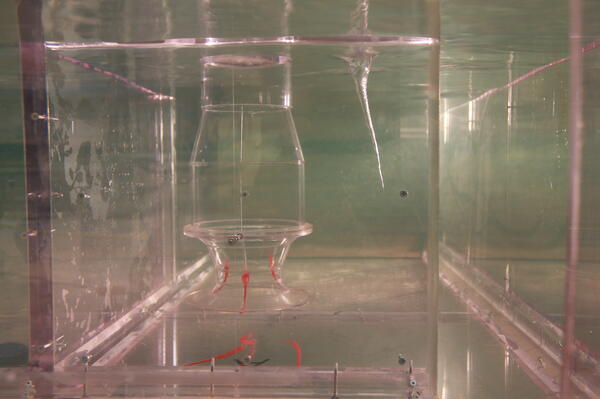
Coupled digital and physical modeling: a hybrid approach to deal with the complexity of air entrainment phenomena in pumping stations.
Development of a vortex in a pumping chamber: a test case for calibration of an OpenFOAM® numerical model
It is essential to characterise hydraulic behaviour, the velocity field and the risk of air entrainment when sizing water intake structures. However, this issue of air entrainment is complex to grasp using a numerical approach: the choice of grid and turbulence model are particularly crucial in reproducing the flows in this type of structure as accurately as possible. For this reason, physical model tests can be performed to acquire data for the calibration and validation of numerical models.
This is what was done in this so-called “hybrid” approach, in which the results from physical model tests of suction at the inlet of a pumping shaft were simulated numerically using the OpenFOAM® software to adjust the calibration parameters of the numerical model.
Calibrating the numerical tool in this way, using measurements taken on a scale model, enabled the numerical modelling specialists in Artelia's Hydraulics teams to obtain some vital information on the parametrisation of turbulent flows in numerical modelling and thus enhance their expertise.
Generally speaking, it is particularly advantageous to develop hybrid modelling in study methodologies in order to draw up the preliminary dimensional design using a numerical approach; this provides a means of testing significant geometrical changes during an initial phase. Optimisation of the hydraulic shapes can then be sought using physical modelling in a second phase.